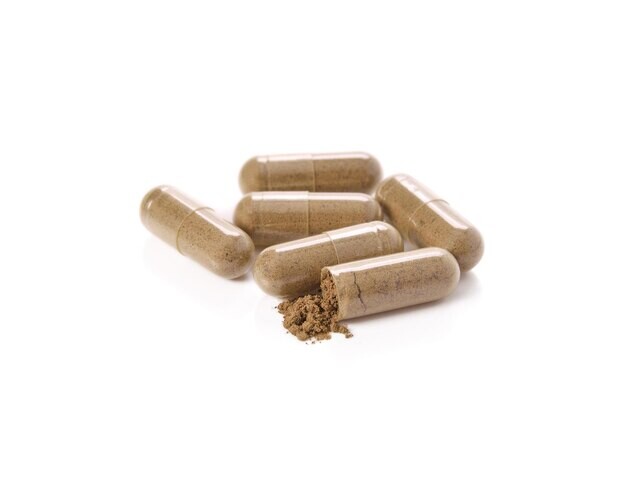
Crafting the Perfect Formula for High-Speed Encapsulation Machines
In the world of manufacturing, precision is the name of the game. Nowhere is this truer than in the operation of high-speed encapsulation machines. These marvels of engineering can produce thousands of capsules per minute, but achieving a flawless end product isn’t just about the machine itself; it’s about the ingredients used in the formulation. In this article, we delve into the critical role of ingredient selection, mesh and particle sizes, and the importance of using top-quality flowing agents to ensure optimal performance while upholding safety standards and regulatory compliance.
The Ingredients Make the Formula
The journey towards creating the perfect capsule starts with ingredient selection. Each component in the formulation contributes to the final product’s quality, consistency, and overall performance. Here are some key considerations when choosing ingredients:
1. Particle Size: The particle size of the ingredients plays a crucial role in preventing quality defects. Inconsistent particle sizes can lead to splits, dents, and capsules that fail to meet quality standards. Uniformity is the key to achieving a flawless finish.
2. Mesh Sizes: Mesh sizes are equally important, as they determine the flowability and consistency of the formula. Using ingredients with the right mesh sizes ensures the efficient flow of materials within the encapsulation machine, preventing clogs and disruptions in production.
3. Formulation Chemistry: The right combination of ingredients is essential for achieving the desired properties in the final product. Compatibility between ingredients, along with their flowability, is critical to prevent issues during the encapsulation process.
Performance and Yield Depend on Formulation
The correct formulation is not just about preventing defects; it also dictates the performance of the encapsulation machine. To achieve the right yield of capsules at the machine’s designed speed, a well-balanced formula is essential. Properly chosen ingredients lead to consistent, high-speed production, maximizing efficiency.
The Role of Flowing Agents
High-speed encapsulation machines operate at rapid rates, which can put a strain on the equipment and the ingredients. To protect the machine from damage and ensure the safety of the end users, the use of quality flowing agents is crucial. These agents enhance flowability, reduce friction, and minimize the risk of ingredients sticking or clumping. A well-formulated blend with superior flowing agents ensures a smoother and safer encapsulation process.
Regulatory Compliance and Customer Safety
In the pharmaceutical and dietary supplement industries, adhering to the latest scientific developments and FDA guidelines is non-negotiable. Choosing ingredients that meet these standards is not only a regulatory requirement but also a commitment to customer safety and product integrity. It ensures that every capsule produced is of the highest quality and can be trusted by consumers.
In conclusion, the importance of selecting the right ingredients for high-speed encapsulation machines cannot be overstated. Mesh sizes, particle sizes, formulation chemistry, and flowing agents are all integral to producing defect-free capsules, optimizing machine performance, and ensuring safety and regulatory compliance. By carefully crafting the ultimate formula, manufacturers can take full advantage of the capabilities of their high-speed encapsulation machines, delivering top-quality products with efficiency and consistency.